KYORAKU TECHNO CO., LTD
Kyoraku TECHNO CO., LTD, Ltd. was established as a production subsidiary of KYORAKU CO., LTD.
This is an injection molding plant for automobiles featuring two-color molding. With the cooperation of Kanto Seisakusho Co., Ltd., a plastic mold manufacturer, we are able to perform integrated production from molds to products.
As a member of the Kyoraku Group, the division of roles between Kyoraku's blow molding and Kyoraku Techno's injection molding creates a system that enables the group to provide more appropriate products to customers.
Company Profile
Trade name | Kyoraku TECHNO CO., LTD Co. Ltd. | ||
---|---|---|---|
location |
2-19, Techno-Plaza,
![]() |
||
Established | November 18, 2009 | ||
Business content | Manufacture and sale of injection molded products | ||
Capital | 50 million yen | ||
Board member |
|
||
Employees | 65 people | ||
Facility |
We have 21 molding machines ranging from 180t to 1300t.
|
Product examples of injection products for automobiles
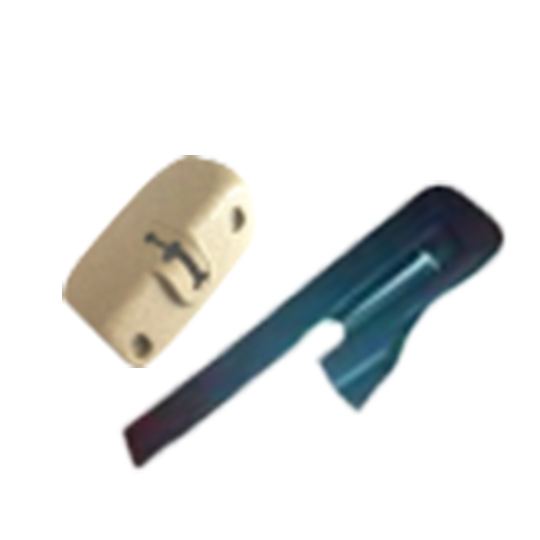
Interior parts
Seat/floor parts, etc. It features a two-color molded product.
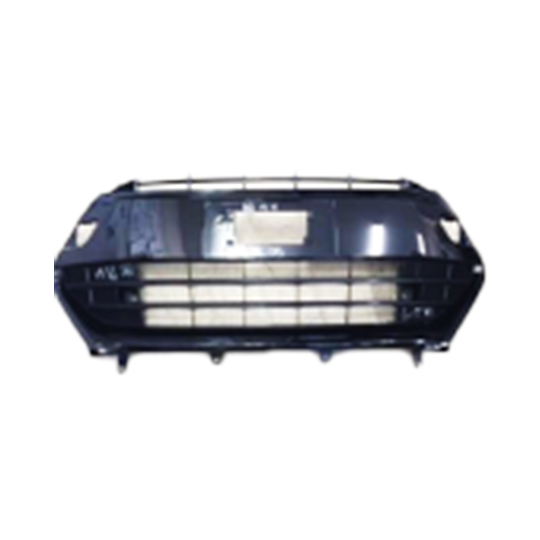
Exterior parts
The lower grill is molded to take in air from the outside.
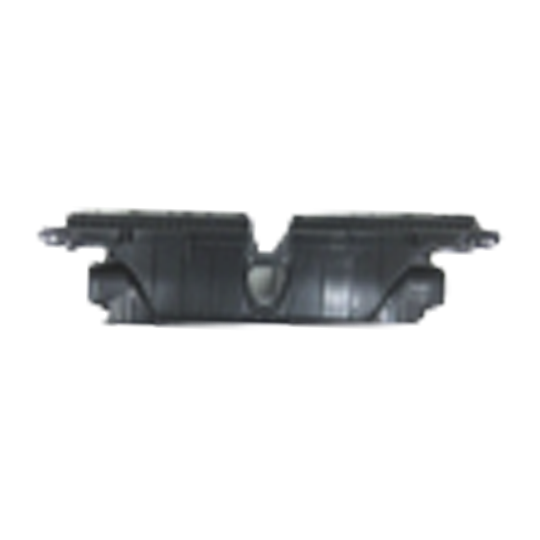
Functional parts
We are molding the duct that is the path of the wind of the air conditioner.
*Painted products are also available.
Two-color molding process
Two-color molding methods are rotational molding, insert molding, and core-back molding. Kyoraku Techno performs rotational molding and insert molding.
We will introduce the insert molding process that is filled with Kyoraku Techno's know-how.
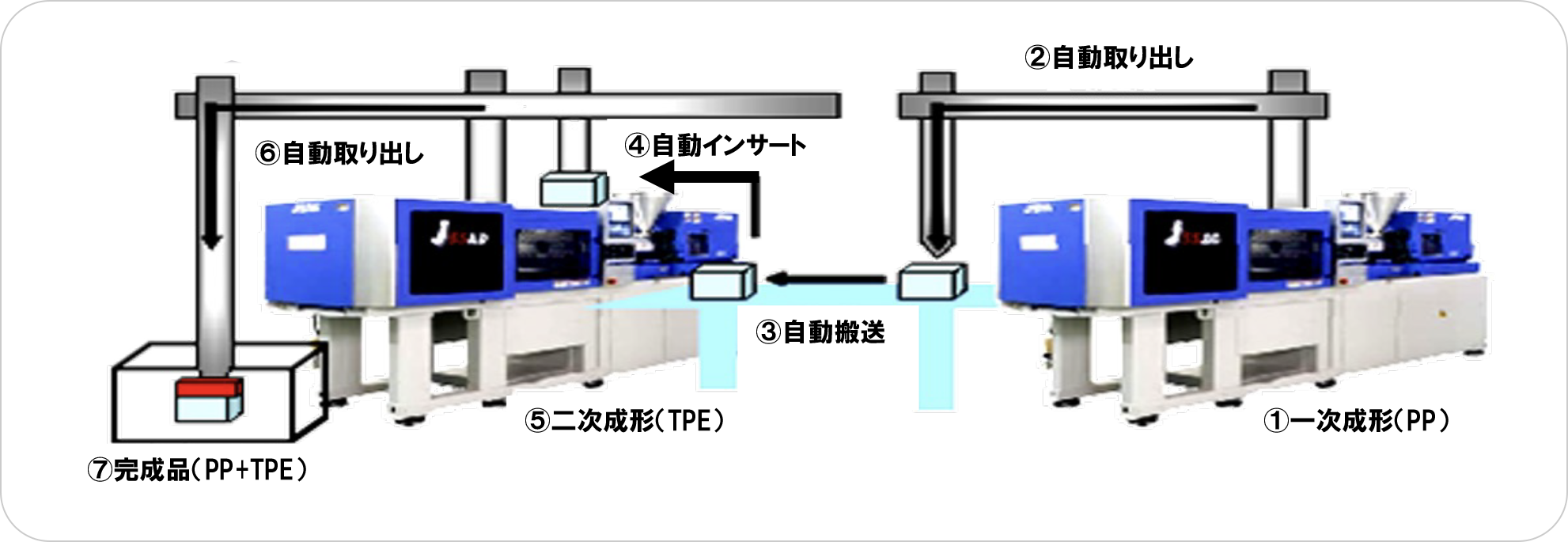
-
Primary molding (PP)
Mold the primary molding (PP) as usual -
Automatic eject
Take out the primary molded product and process the gate -
Automatic transfer
The primary molded product is slide-conveyed to the secondary molding machine. -
Automatic insert
The secondary take-out machine picks up the primary molded product and inserts the primary molded product into the secondary mold. -
Secondary molding (TPE)
Perform secondary molding (elastomer) -
Automatic eject
Take out the integrally molded secondary molded product (finished product) -
Completion (PP+TPE)
The finished product is placed in a specified position, finished, inspected, and boxed.