Blow molding/FLP
- Blow molding
- Epidermis
- hollow body
- Insert molding
- Large molding
- multilayer container
- Gas barrier property
- Oxygen barrier
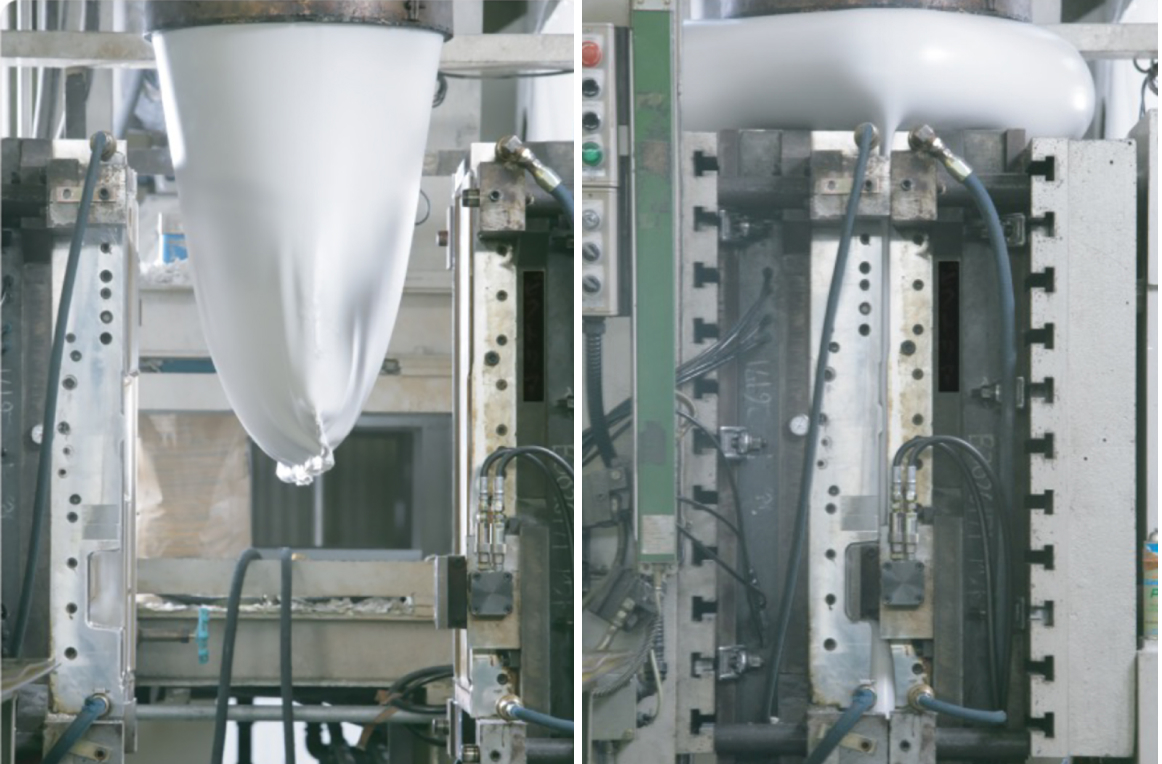
What is blow molding/FLP?
In blow molding, plastic pellets (granules) are melted, kneaded, and extruded by an extruder, passed through a high-temperature metal cylinder (head), and the molten resin (parison) is molded into a cylindrical shape. In this method, the parison is sandwiched between molds, a needle is inserted, high-pressure gas is blown in, and the parison is pressed against the inner surface of the mold, and then cooled to form a hollow body.
The molding method developed by incorporating our original know-how into the blow molding technology is a technology called FLP (Fabric Laminated Plastics), which allows carpet to be attached without adhesives, so it is low cost and environmentally friendly. Gentle technology.
Advantages of blow molding and FLP
Suitable for molding hollow bodies such as containers and tanks
It is a technology originally developed based on the molding of glass bottles, and is good at creating inflated shapes.
Suitable for medium to small lot production
Mold cost is generally cheaper than injection molding, and it can be handled even if the number of production is small.
Easy to deal with large products
By utilizing the hollow shape for large molding, it is possible to handle light and large products.
FLP technology can be used to integrally mold the surface of carpets, etc.
Since the fabric is attached to the product in the mold at the same time as blow molding, it is possible to obtain an integrated product at low cost and with less environmental impact without using adhesives.
Technology introduction
Industrial blow molding
When molding a particularly large product in blow molding, the melted resin is temporarily stored in a part called an accumulator from the extruder, and then it is pushed out at once using a mechanism such as hydraulic pressure to mold a large product. We have a molding machine that can extrude resin up to about 50 kg (PE).
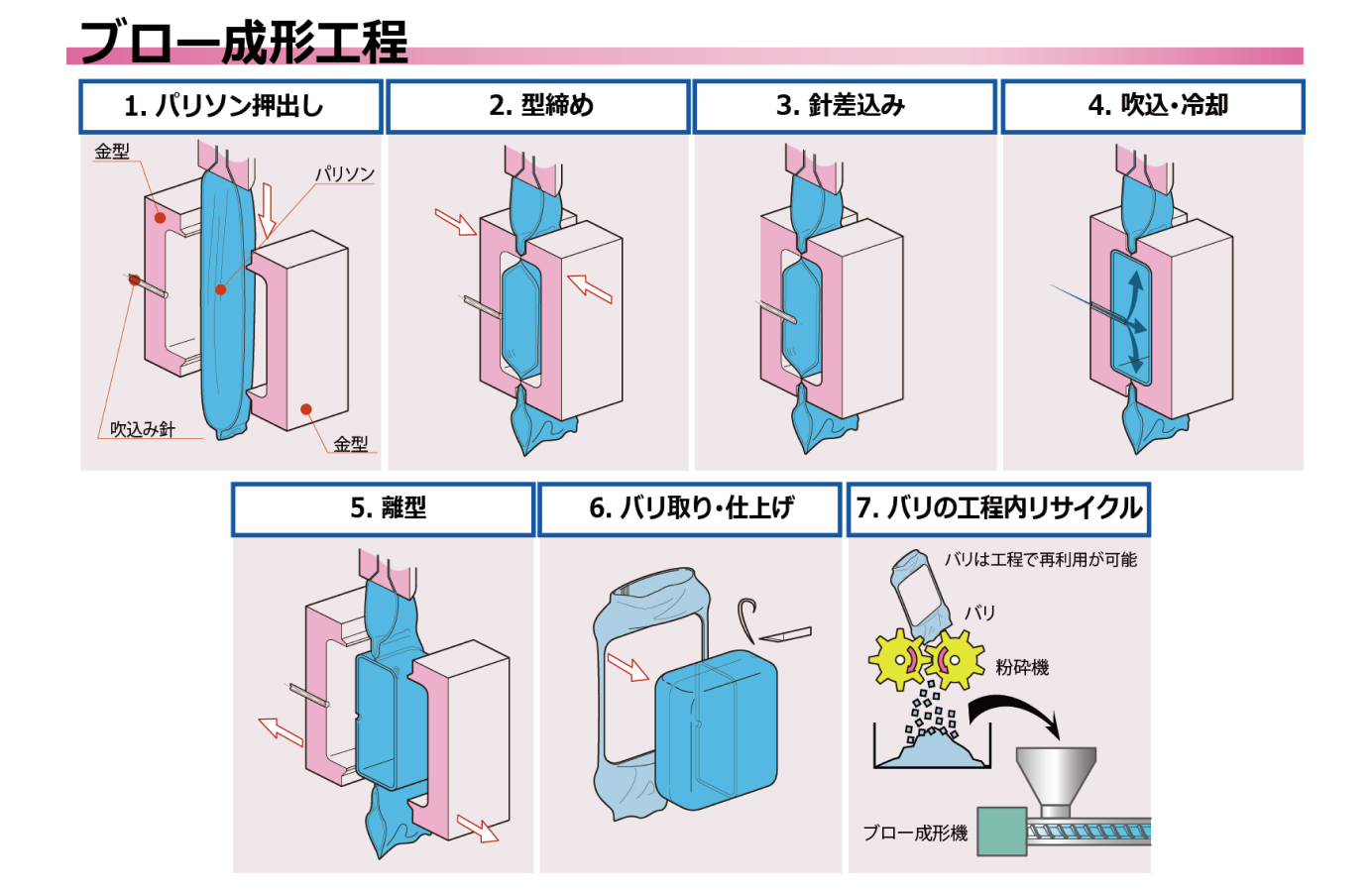
Product examples
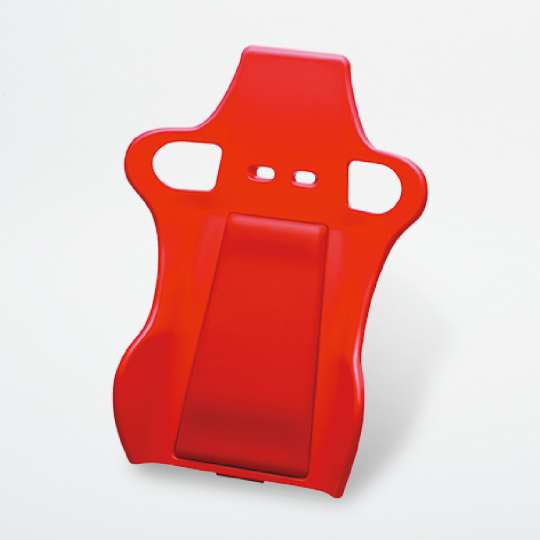
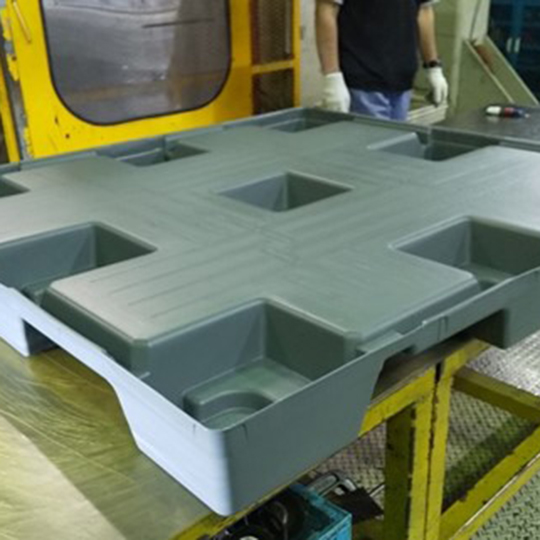
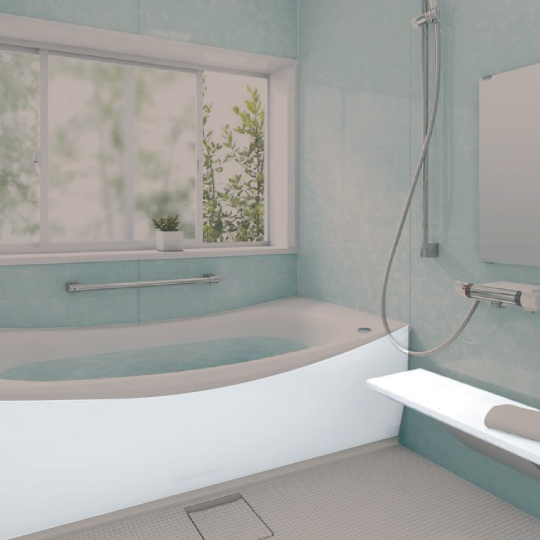
Shuttle Method Blow Molding
The parison is continuously extruded, and when it reaches a certain length, it is sandwiched between dies and cut at the same time, and the dies are moved to the blowing section. In this method, the nozzle in the blowing part is inserted into the hollow part of the parison, and high-pressure gas is blown into the mold so that it adheres to the inner surface of the mold, cooling the molten resin, and molding the hollow body. Normally, resin pieces (Flash) are generated on the top and bottom, but they can be separated automatically. It is called a Shuttle Method Blow Molding machine because it repeats the mold movement to the left and right.
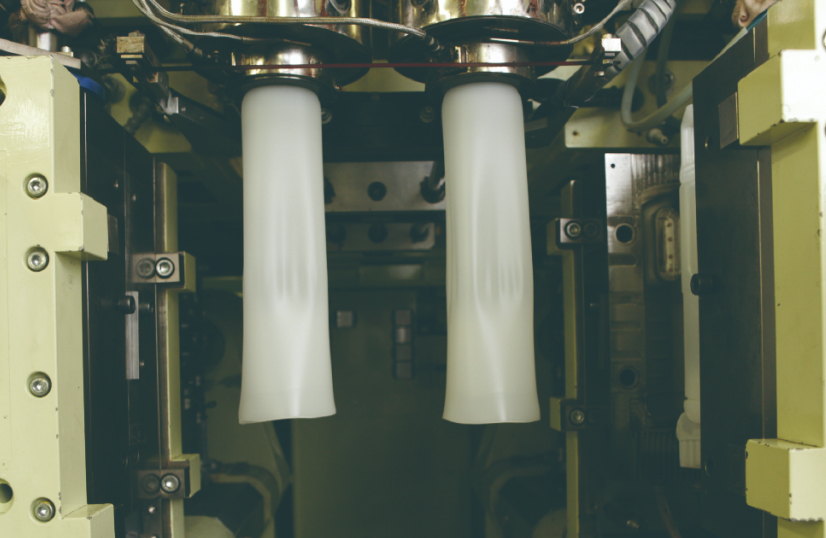
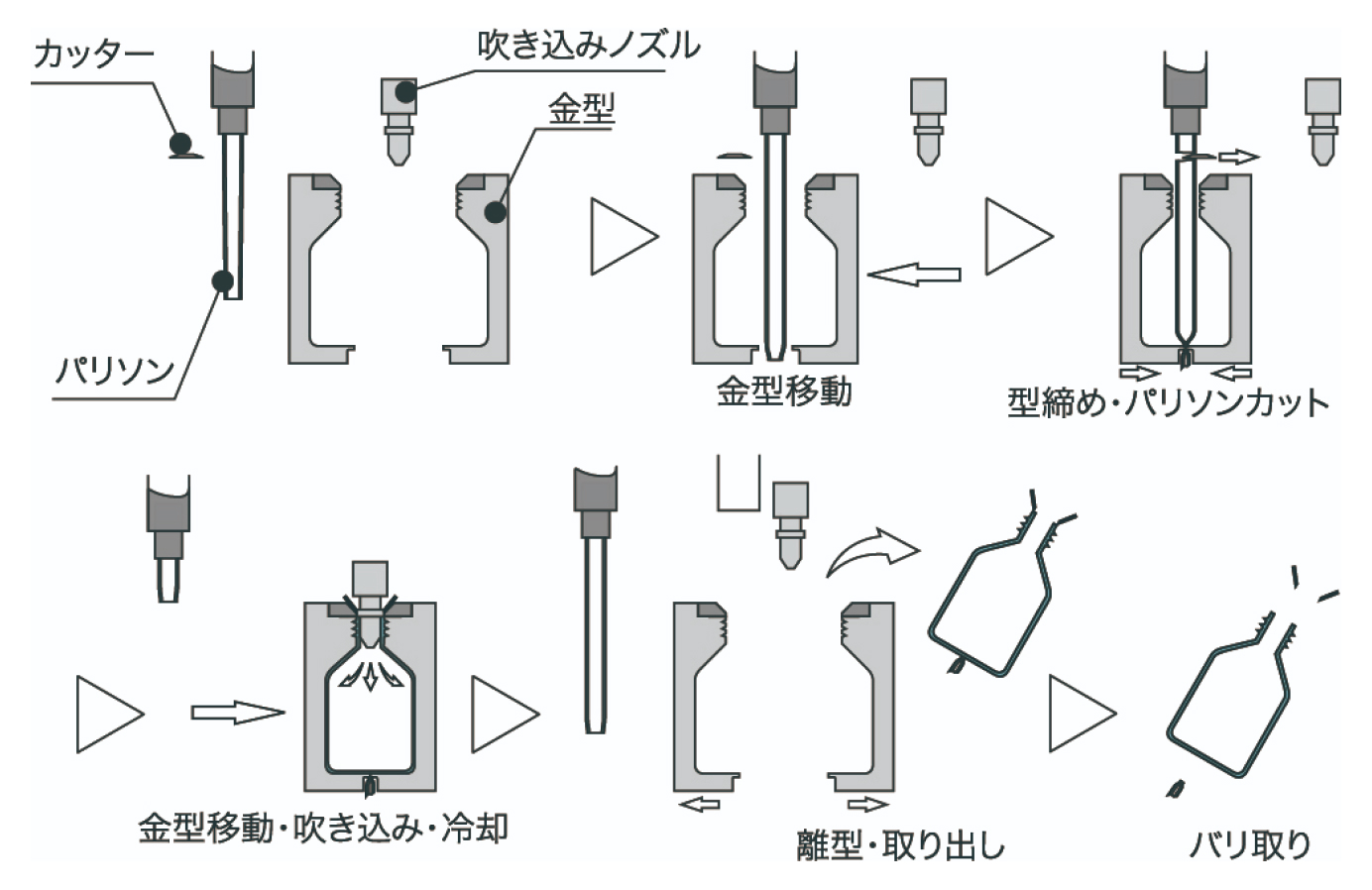
Product examples
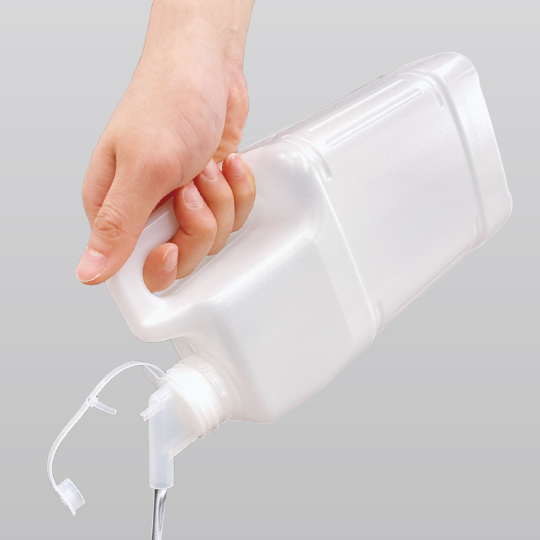
Rotary Method Blow Molding
A dozen or so molds are placed on a disk, and the molds are opened and clamped continuously, and the parison is sandwiched between them. The parison is brought into close contact with the inner surface of the mold by gas pressure, and the molten resin is cooled to form a hollow product. It is called a Rotary Method Blow Molding machine because it molds while continuously rotating the mold.
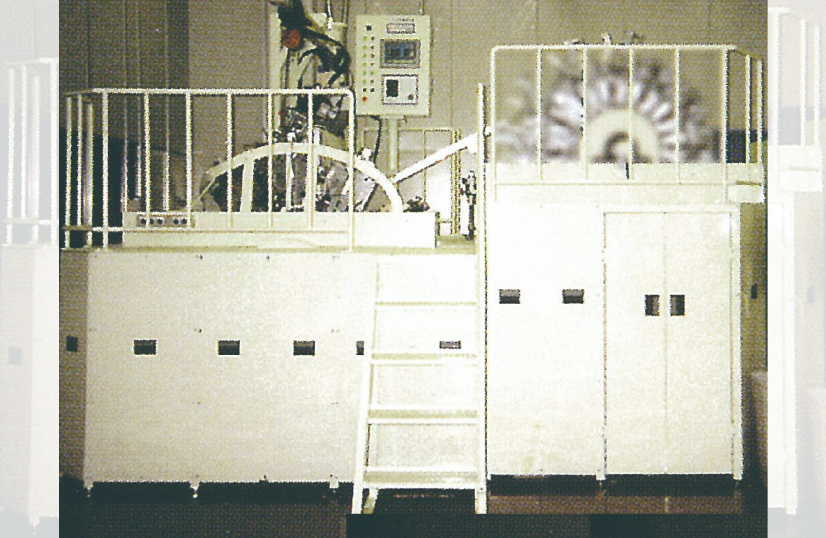
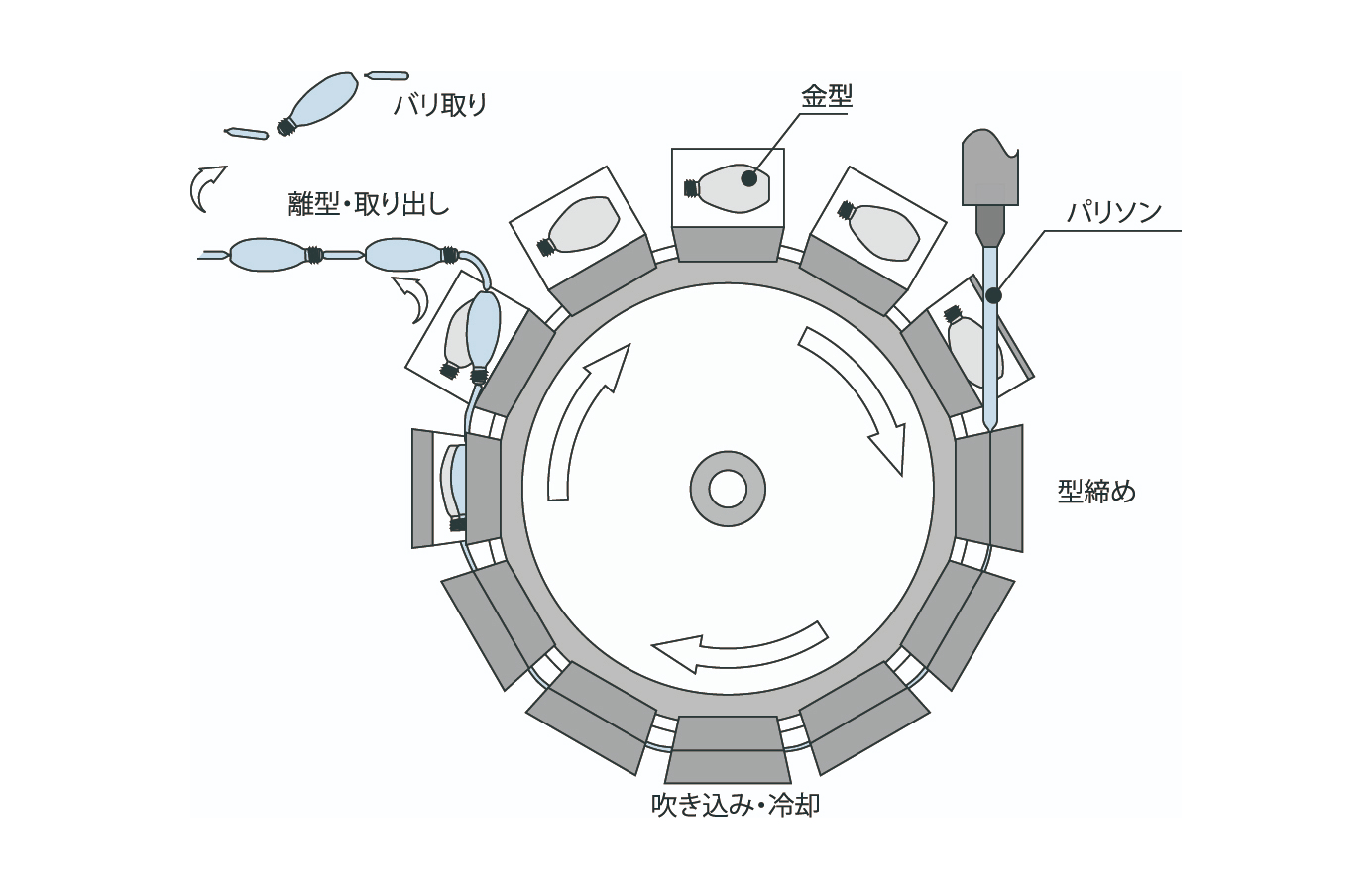
Product examples
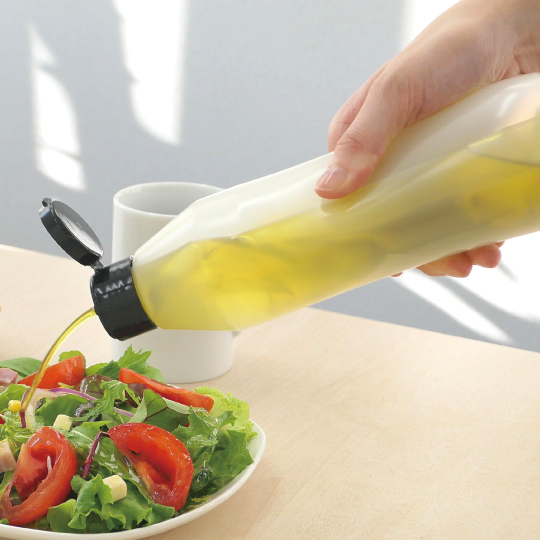
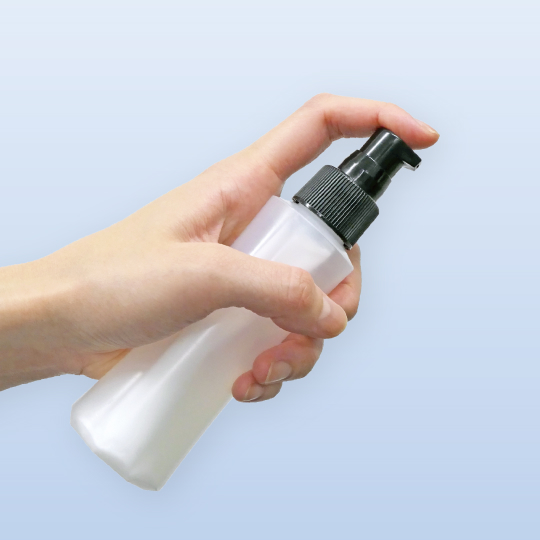
FLP (Non-Woven Integral Molding)
FLP (Fabric Laminated Plastic) applies blow molding technology to set the fabric in advance in the mold and attach the fabric to the product in the mold at the same time as the blow molding. Fabric can be attached to the product surface without using adhesives, at low cost and with less environmental impact. In addition, if the fabric and the product are made of the same material, they can be recycled together, further reducing the burden on the environment.
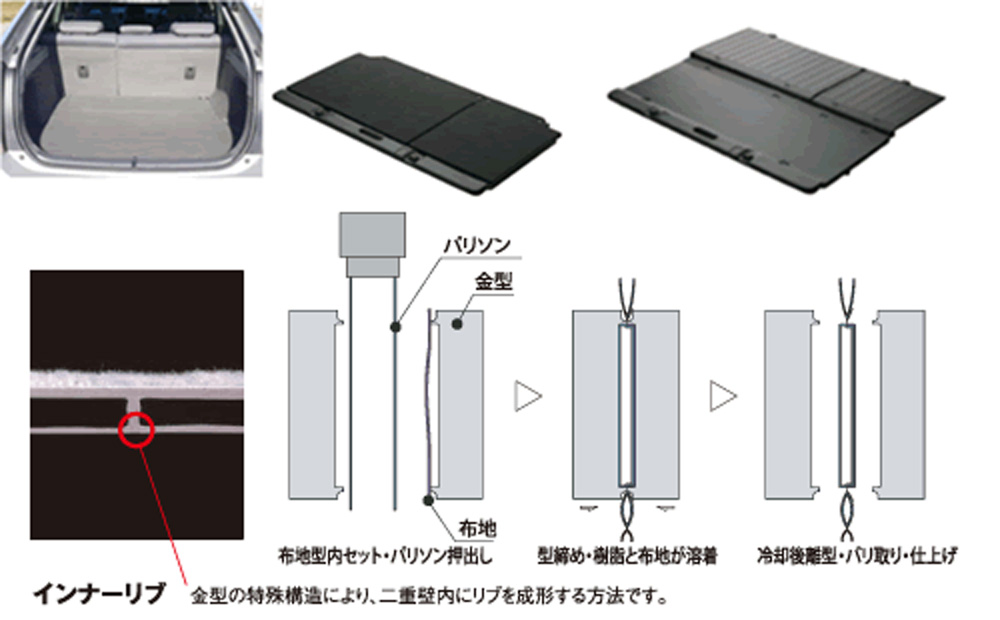
Product examples
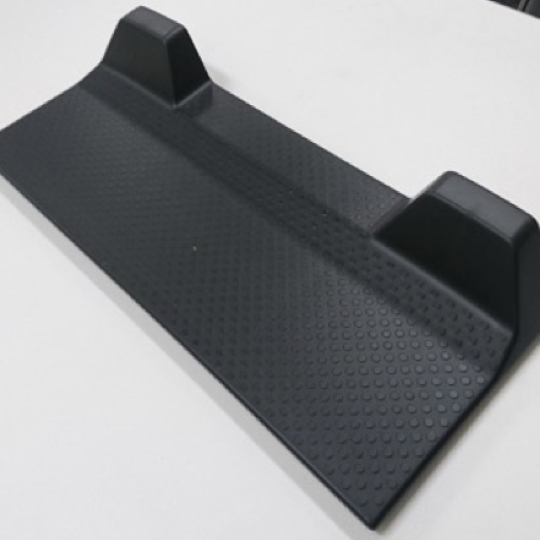
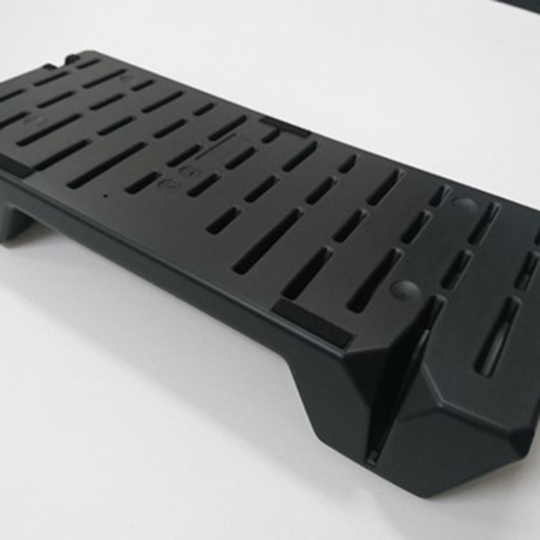
Do you have anyworriesorconcerns ?
- I have an idea, but I don't know how to implement it...
- I don't have knowledge or expertise in plastic products...
- Where can i make it
Our company specializes in blow molding, which we have cultivated over many years, and we are working on further developing new molding methods and product development by incorporating our original know-how.
We also have knowledge and experience in other plastic molding methods such as injection molding, extrusion molding, and vacuum pressure molding.
We also handle a wide range of plastic products, such as automobile parts, general molded products, food and medical containers, and films, so we can also accept consultations on manufacturing with plastic.
As a comprehensive plastics company, we provide total support for the manufacturing of our customers by using our facilities and staff to handle all processes from product design to development and mass production.
Inquiries/Consultation
For inquiries and consultations
From the form below,
Please feel free to contact us.
We can also meet online.